

Expectation and deliverables from the team.A clear description of the problem helps the team come up with more relevant solutions.Ĭommunicate the scope of the problem that the team is working on and get the team focused. Organizations need to become better at asking the right questions so that they tackle the right problems.ĭefine the problem as objectively as possible. Well-defined problems lead to breakthrough solutions. Minutes of the meeting must include agenda, actions decided, responsibility, target date. The team leader must schedule meetings periodically to review the progress of the 8D project and discuss activities related to any delays.The team leader must define the roles of each team member and bring it on paper.Supplier Quality, Electrical Engineering, Mechanical Engineering, Manufacturing Engineering, Operations, Field Service, Technical Support, Marketing, Application Engineering, etc…) – people who have practically experienced the problem and understand the pain it causes. A subject expert is one who has the domain expertise.He/she is expert in the domain to which problem belongs.He/she guides the team for appropriate implementation of 8D methodology. Quality Engineering) – A person who has the technical know-how of the 8 disciplines. Team leader act’s as a binding force amongst all team members. Quality engineering or Product Manager) – The person who coordinates the entire 8D project through-out all of its 8 disciplines.
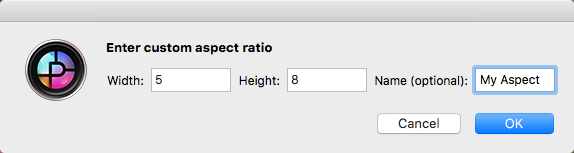
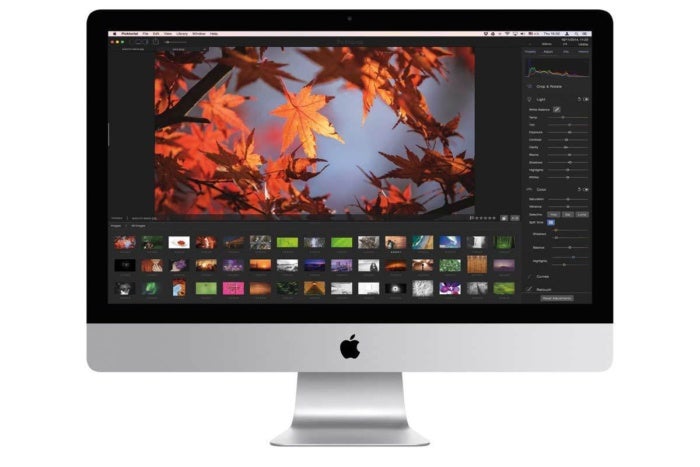
He is responsible for proving final approval for changes if he agrees with findings.
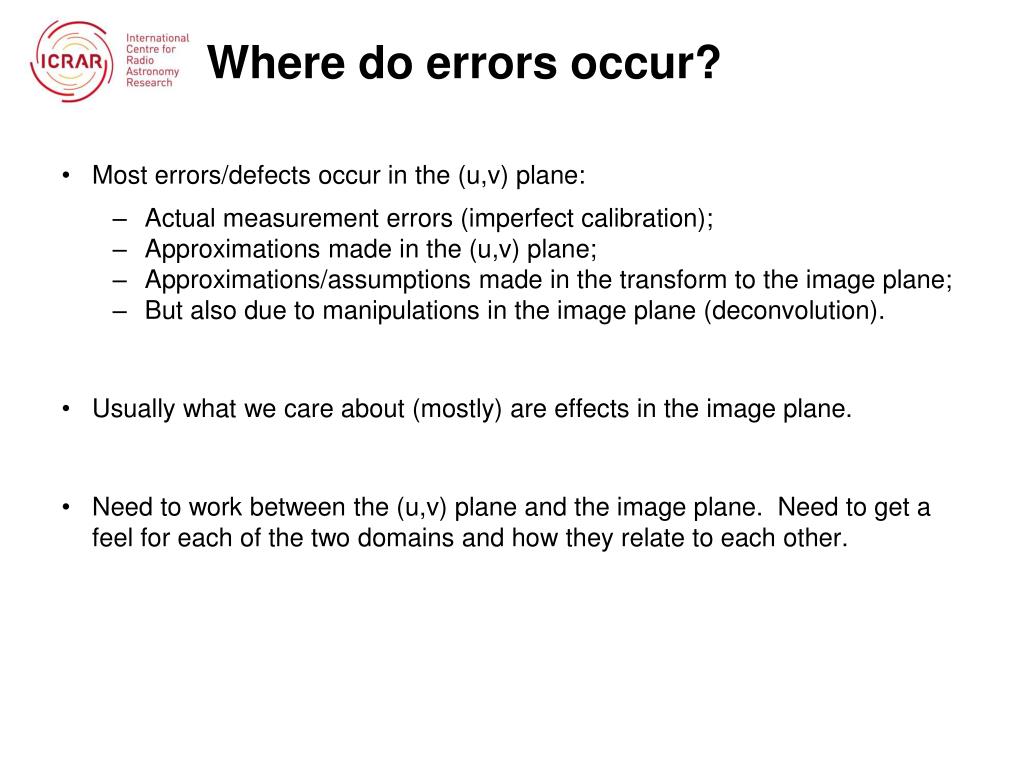
Defining roles and expectation in advance makes the process quicker and more efficient. Roles and desirable outputs of each member have to be clearly defined. Because the team without captain means, everybody is captain, which creates chaos and hampers the process. Somebody should be adopted as a team leader. It should include all departments like Production, Development, Quality, etc.Ĭombination of multiple experiences, skill set, and knowledge base helps take the multidimensional perspective of the problem in hand. D1-Create a Teamīuilding a relevant team is the first step to this problem-solving process. The 8D Report consists of 8 disciplines that describe corrective measures based on the statistical analysis of the problem. It helps provide structure to our problem-solving process.ĭue to its certain sequence, it helps inculcate multiple perspectives.Īlso, this process helps back our actions with statistical data. Checking the complete history of the problem.ĨD methodology consists of 8 steps or 8 Disciplines.Is it a repetitive problem? if yes what problem-solving methodology was used and why it failed?.THINGS TO CHECK BEFORE IMPLEMENTING 8D METHODOLOGY The 8D method is also known as Global 8D, Ford 8D or TOPS 8D.ĨD Methodology follows the PDCA approach.D1 to D5 is covered under the planning phase, D6- constitutes Do phase, D7 and D8 constitute check and act phase. It helped standardize the problem-solving process throughout the automotive industry.Īlthough this method was originated by the US military, generally it is referred that Ford originated it, since they used it on such a large scale and made it popular. It was used for all problem-solving activities. ORIGINĨD method was first used as a part of Team Oriented Problem Solving (TOPS) in the United States during world war-2.ĨD Methodology was made popular by Ford in 1990s. The 8D problem-solving model helps establish corrective and preventive action to avoid problems in the future. The purpose of the 8D methodology is to identify, correct, and eliminate recurring problems. Moreover, this tool can be used as a part of continuous improvement of any product or process. It covers containment till prevention of problem recurrence. It provides structure to the problem-solving process.8D methodology gives a hollistic approach to problem-solving. But it has also been successfully applied in healthcare, retail, finance, government, and manufacturing.ĨD is a problem-solving methodology, useful for finding a short term fix and permanent solution to your product or process problems. It is a problem-solving approach typically employed in the automotive industry by quality engineers. D6 – Implement Permanent corrective actionsĨD stands for eight disciplines (8D) model.Criteria for choosing the best solution.THINGS TO CHECK BEFORE IMPLEMENTING 8D METHODOLOGY.
